Focus Microwaves - Manual Tuners
Model |
Min Frequency |
Max Frequency |
Type |
Datasheets |
MMT304 | 0.4 GHz | 3.0 GHz | Manual | |
MMT306 | 0.6 GHz | 3.0 GHz | Manual | |
MMT308 | 0.8 GHz | 3.0 GHz | Manual | |
MMT316 | 1.6 Ghz | 3.0 GHz | Manual | |
MMT606 | 0.6 GHz | 6.0 GHz | Manual | |
MMT704 | 0.4 GHz | 7.0 GHz | Manual | |
MMT708 | 0.8 GHz | 7.0 GHz | Manual | |
MMT716 | 1.6 GHz | 7.0 GHz | Manual | |
MMT808 | 0.8 GHz | 8.0 GHz | Manual | |
MMT1804 | 0.4 GHz | 18.0 GHz | Manual | |
MMT1808 | 0.8 GHz | 18.0 GHz | Manual |
More Product Information
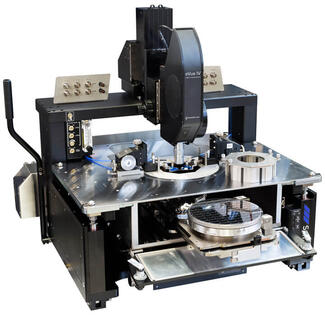
-
Re-configurable for DC, RF, mmW, FA, WLR and more
-
Thermal range: -60˚C to 300˚C available
-
Upgrade path to meet your future needs
-
Stable and repeatable measurements over a wide thermal range
-
Moisture-free, light-tight and EMI-shielded test environment with MicroChamber® technology
-
Advanced EMI-shielding with PureLine with AttoGuard technologies
-
Best solution for low-noise and 1/f measurements
-
Minimize AC and spectral noise
-
Minimizes settling times for efficient measurements, without compromising accuracy over full thermal range
-
Locking roll-out stage
-
Innovative microscope remote control
-
Intuitive ergonomic stage controls
-
Quick, safe, and comfortable wafer access
-
Easy on-wafer navigation
-
Fast setup and test data gathering
-
Dedicated Velox version for manual probe stations
-
AugmentedAlign tool with on screen markers for improved RF measurement accuracy
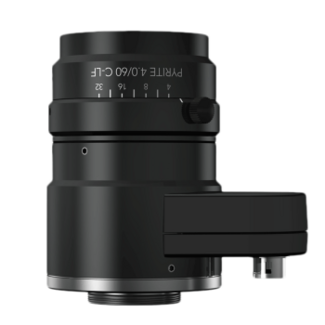
- Focus tunable liquid lens included
- Large working distance range
- Fast focus within milliseconds
- Large image circle
-
Auto gain (manual gain control: 0 to 32 dB)
-
Auto exposure (manual exposure control: 10 µs to 26.8 s)
-
Auto white balance (GT1660C only)
-
Binning (horizontal and vertical)
-
Color correction, hue, saturation (GT1660C only)
-
Column defect masking
-
Decimation X/Y
-
Gamma correction
-
Three look-up tables (LUTs)
-
Region of interest (ROI), separate ROI for auto features
-
Reverse X/Y
-
P-Iris and DC-Iris lens control
-
Event channel
-
Image chunk data
-
IEEE 1588 Precision Time Protocol (PTP)
-
RS232
-
Storable user sets
-
StreamBytesPerSecond (bandwidth control)
-
Stream hold
-
Sync out modes: Trigger ready, input, exposing, readout, imaging, strobe, GPO
-
Tap mode switchable in Vimba Viewer 2.0 or later (four-tap, one-tap)
-
Temperature monitoring (main board and sensor board)
-
Trigger over Ethernet (ToE) Action Commands

-
Type APS-H CMOS sensor
-
IEEE 1588 PTP
-
Power over Ethernet
-
4.59 fps at full resolution
-
Extended near-infrared (GT5120NIR) model
-
GigE Vision interface with Power over Ethernet
-
Screw mount RJ45 Ethernet connector for secure operation in industrial environments
-
Supports cable lengths up to 100 meters (CAT-6 recommended)
-
Trigger over Ethernet Action Commands allow for a single cable solution to reduce system costs
-
Comprehensive I/O functionality for simplified system integration
-
Planarity adjusted (PA) EF Lens Mount (option -18) for electronic control of aperture and autofocus
-
Easy camera mounting via standard M3 threads at all sides and 1/4-20 tripod mounting hole
-
Easy software integration with Allied Vision's Vimba Suite and compatibility to the most popular third party image-processing libraries.
-
Enhanced Defect Pixel Correction feature with a new Defective Pixel List Manager tool that allows you to load different user defined defective pixel lists to match your application and optimize the life cycle of the camera
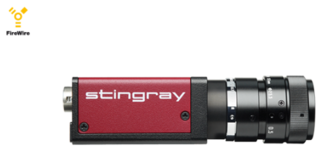
-
High SNR mode (up to 24 dB better signal-to-noise ratio)
-
Low-noise binning mode
-
Shading correction
-
Defect pixel correction
-
Area of interest (AOI), separate AOI for auto features
-
Binning
-
Sub-sampling
-
Auto gain (manual gain control: 0 to 24.4 dB)
-
Auto exposure (48 µs to 67 s)
-
Auto white balance
-
Look-up table (LUT)
-
Hue, saturation
-
Color correction
-
Local color anti-aliasing
-
Reverse X/Y
-
Deferred image transport
-
Trigger programmable, level, single, bulk, programmable delay
-
Sequence mode (changes the camera settings on the fly)
-
SIS (secure image signature, time stamp for trigger, frame count etc.)
-
Storable user sets
-
Camera and IEEE 1394b cable (other configurations on request)
-
High SNR mode (up to 24 dB better signal-to-noise ratio)
-
Low-noise binning mode
-
Smear reduction
-
Shading correction
-
Defect pixel correction
-
Area of interest (AOI), separate AOI for auto features
-
Binning
-
Decimation
-
Auto gain (manual gain control: 0 to 24 dB)
-
Auto exposure (129 µs to 67 s)
-
Auto white balance
-
Look-up table (LUT)
-
Hue, saturation, color correction
-
Reverse X
-
Deferred image transport
-
Trigger programmable, level, single, bulk, programmable delay
-
Sequence mode (changes the camera settings on the fly)
-
SIS (secure image signature, time stamp for trigger, frame count)
-
Storable user sets
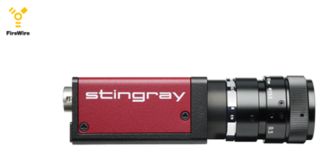
-
High SNR mode (up to 24 dB better signal-to-noise ratio)
-
Low-noise binning mode
-
Shading correction
-
Defect pixel correction
-
Area of interest (AOI), separate AOI for auto features
-
Binning
-
Decimation
-
Auto gain (manual gain control: 0 to 24.4 dB)
-
Auto exposure (74 µs to 67 s)
-
Auto white balance
-
Look-up table (LUT)
-
Hue, saturation
-
Color correction
-
Local color anti-aliasing
-
Reverse X/Y
-
Deferred image transport
-
Trigger programmable, level, single, bulk, programmable delay
-
Sequence mode (changes the camera settings on the fly)
-
SIS (secure image signature, time stamp for trigger, frame count etc.)
-
Storable user sets
- Camera and IEEE 1394b cable (other configurations on request)
-
Auto gain (manual gain control: 0 to 26 dB; 1 dB increments)
-
Auto exposure (18 µs to 126 s; 1 µs increments)
-
Black level (offset)
-
Decimation
-
Gamma correction
-
Three look-up tables (LUTs)
-
Pixel defect masking
-
Piecewise Linear HDR mode
-
Region of interest (ROI), separate ROI for auto features
-
Reverse X/Y
-
Auto-iris (video type)
-
Event channel
-
Image chunk data
-
IEEE 1588 Precision Time Protocol (PTP)
-
Storable user sets
-
StreamBytesPerSecond (bandwidth control)
-
Stream hold
-
Sync out modes: Trigger ready, input, exposing, readout, imaging, strobe, GPO
-
Temperature monitoring (main board)
-
Trigger over Ethernet (ToE) Action Commands


Focus Microwaves
Focus Microwaves is a pioneering engineering company, built around the innovations of its founder Dr. Christos Tsironis who developed his first manual tuner in 1973 and is the inventor of most existing electro-mechanical tuner families. The success of Focus is based on the engineering and manufacturing skills of its highly motivated and experienced team of engineers and technicians, who have been trained and encouraged to develop new technologies. In addition, listening to our customers needs and insights helps us discover and develop new and measurement methods on an ongoing basis, relentlessly pushing the limits of what is possible.
From humble beginnings in 1988, Focus has become the main supplier of advanced Load Pull and Noise Tuner Systems. Our mission is to provide effective, reliable and innovative solutions for non-50 Ohm testing (Noise and Load Pull) of RF microwave transistors, thus enabling our customers to compete in the marketplace with better designs and to advance the understanding and knowledge of the field.
Contact Details
Focus Microwaves Inc. Main Head Office
4555 Chem. du Bois-Franc, Saint-Laurent, QC H4S 1A8, Canada
Phone: +1-514-684-4554
Test & Measurement
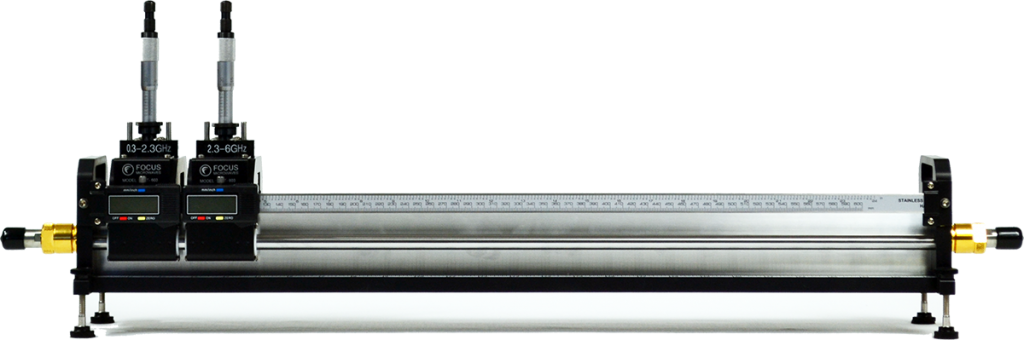